Mastering Plastic Mold Tooling: A Comprehensive Guide for Metal Fabricators
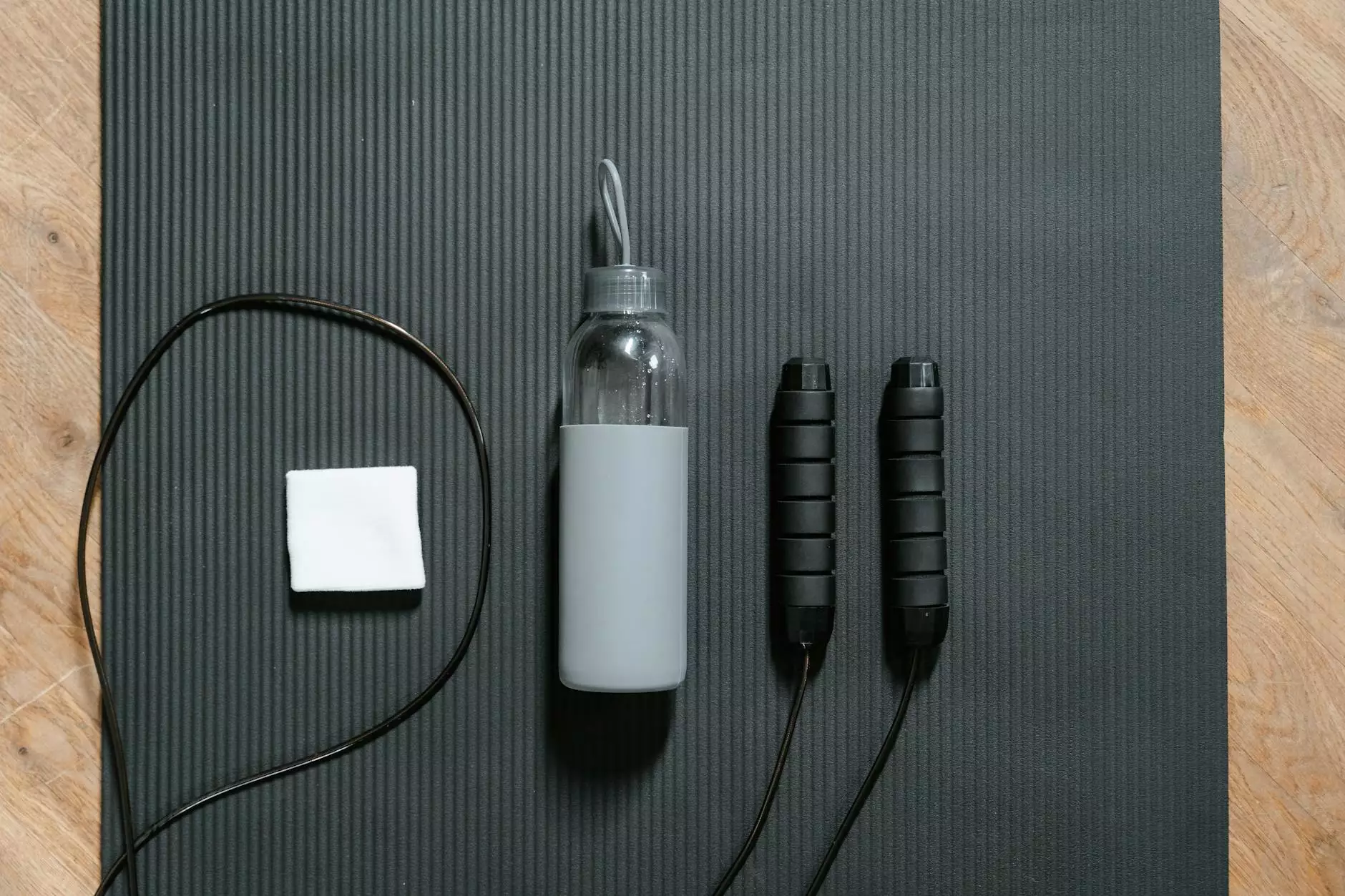
In today's fast-paced manufacturing environment, plastic mold tooling plays a pivotal role in creating high-quality products efficiently. For metal fabricators and manufacturers, understanding the nuances of plastic mold tooling can significantly enhance production capabilities, reduce costs, and improve overall product quality. This article delves into the details of plastic mold tooling, its applications, advantages, and best practices in the industry.
What is Plastic Mold Tooling?
Plastic mold tooling refers to the process of designing and manufacturing molds that are utilized for shaping plastic products. It is an essential phase in plastic injection molding, where a thermoplastic material is melted and injected into a mold to create various products ranging from simple containers to complex automotive components.
The Importance of Tooling in Manufacturing
Effective tooling is crucial for achieving precision, consistency, and quality in manufacturing. Here are several key reasons why tooling is important:
- Quality Control: Properly designed molds ensure that products meet specific quality standards.
- Cost Efficiency: High-quality molds reduce production errors and waste, leading to lower operational costs.
- Production Speed: Efficient tooling allows for faster turnaround times in production runs.
- Flexibility: Custom molds can be designed for various applications, catering to diverse product lines.
Types of Plastic Mold Tooling
Understanding the different types of plastic mold tooling is paramount for choosing the right approach for your manufacturing needs. The following are the most common types:
1. Injection Molds
Injection molds are the most common type of molds used in plastic molding. The process involves heating plastic resin until it melts and then injecting it into a mold cavity. This method allows intricate designs and high-volume production.
2. Blow Molds
Blow molding is used to create hollow plastic products. The process involves inflating a heated tube of plastic inside a mold to form items such as bottles and containers.
3. Compression Molds
This method is primarily used for manufacturing thermosetting plastics. It involves placing a pre-measured amount of material into a mold and applying heat and pressure to form the final product.
4. Rotational Molds
Rotational molding is employed for producing large, hollow items. In this process, a mold is rotated around a central axis while heated, enabling the plastic to coat the interior surface evenly.
Benefits of Plastic Mold Tooling
Investing in sophisticated plastic mold tooling offers numerous advantages, particularly for metal fabricators:
- Enhanced Precision: Modern technologies allow for the creation of highly detailed molds, resulting in better product accuracy.
- Reduced Lead Times: Efficient tooling methods expedite the production timeline, enabling faster market entry.
- Sustainability: Advanced tooling processes minimize material waste, aligning with eco-friendly manufacturing practices.
- Increased Flexibility: The ability to produce a wide range of products with varied designs translates to higher market adaptability.
Plastic Mold Tooling Process
The process of plastic mold tooling is meticulous and involves several stages:
1. Design Phase
The initial stage involves the creation of detailed mold designs using Computer-Aided Design (CAD) software. This stage is critical for ensuring that the mold will meet the specifications required for the final product.
2. Prototype Development
After design approval, a prototype of the mold is often produced. This step allows for testing and adjustments before mass production, ensuring any necessary changes can be made early in the process.
3. Manufacturing the Mold
The actual mold is manufactured using high-quality materials, usually steels or aluminum, which are capable of withstanding the pressures and temperatures involved in injection molding.
4. Testing and Quality Control
Once the mold is completed, it undergoes rigorous testing to ensure it meets all operational standards. Quality control checks are essential to prevent future production issues.
5. Production Run
Once testing has confirmed that the mold is functioning correctly, it is put into production, where plastic products are created at scale.
Challenges in Plastic Mold Tooling
While plastic mold tooling offers numerous benefits, there are also challenges that metal fabricators must be aware of, including:
1. High Initial Costs
The upfront investment for high-quality molds can be significant. However, considering the long-term savings and benefits, this initial cost is often justified.
2. Complexity of Design
Creating highly detailed and complex molds can be challenging and may require advanced engineering and design capabilities.
3. Maintenance and Repairs
Molds require regular maintenance to ensure they function correctly over time. This includes repairing any wear and tear that occurs during use.
Best Practices for Effective Plastic Mold Tooling
To maximize the efficiency and quality of your plastic mold tooling, consider the following best practices:
1. Invest in High-Quality Materials
Using superior materials for molds will increase their lifespan and reduce the frequency of repairs and replacements.
2. Utilize Advanced Design Software
Investing in state-of-the-art CAD software can streamline the design process, allowing for precise and accurate mold designs.
3. Maintain Open Communication with Design Teams
Collaboration between engineering, design, and production teams is crucial for ensuring molds are developed effectively and meet production needs.
4. Regularly Schedule Maintenance
Establishing a routine maintenance schedule for your molds can preemptively address wear issues and prolong the lifespan of your tooling.
Conclusion: The Future of Plastic Mold Tooling in Metal Fabrication
As manufacturing continues to evolve, the demand for advanced plastic mold tooling will only increase. For metal fabricators, embracing innovative tooling technologies and methodologies can open new avenues for efficiency, flexibility, and product innovation.
By understanding the complexities and advantages of plastic mold tooling, businesses can position themselves as leaders in the market, ultimately driving growth and success.
For more information on plastic mold tooling and how it can benefit your business, visit deepmould.net.